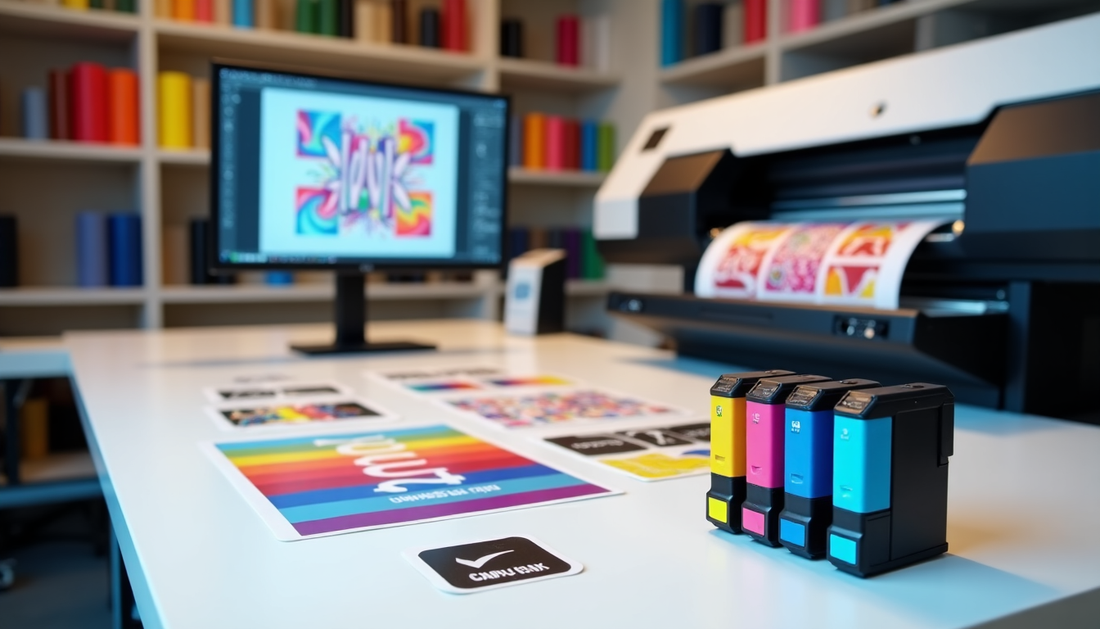
How to Prepare Perfect CMYK Files for Sticker Printing: A Printer's Guide
Share
CMYK represents the foundation of accurate color reproduction in sticker printing. Designers often experience unexpected color changes as their designs reach the printer. RGB provides more vibrant colors, particularly bright and neon shades. However, physical printing requires CMYK conversion to achieve accurate results.
Successful sticker printing requires a good understanding of CMYK's subtractive color model. The process starts with a white background and uses four primary inks - Cyan, Magenta, Yellow, and Key (Black). These inks work together to create the colors in your final printed stickers. Your printed stickers will match your original design better if you convert files to CMYK before submitting them.
This piece walks you through the detailed steps to prepare perfect CMYK files for sticker printing. You will discover ways to prevent common color problems and manage color profiles. The guide also helps ensure consistent results on different printing materials. Small print tests before large orders are recommended, and you'll learn the exact steps to make these tests work.
Understanding CMYK Color Requirements for Stickers
Print professionals choose CMYK color mode because it gives better results when making stickers. Digital displays work with RGB, but CMYK uses a different approach. It layers ink dots to create exact color combinations on white surfaces.
Key Differences Between RGB and CMYK for Print
Screen colors look bright because RGB uses light to create vivid hues. CMYK takes a different path with physical inks - Cyan, Magenta, Yellow, and Black that absorb light to produce colors. This basic difference explains why RGB files sent straight to print often create unexpected color changes or fail during processing.
Most print shops won't accept RGB files because their equipment can't properly read these color definitions. The conversion from RGB to CMYK takes extra time and might not look right in the end.
Color Gamut Limitations in Sticker Printing
CMYK color range has some limits that you'll notice in sticker printing. The most vibrant prints come from mixing 100% cyan, magenta, and yellow. These colors still won't pop as much as what you see on your screen.
The best way to get great sticker prints:
- Design in CMYK mode from the start
- Pick colors using physical matching books
- Run small test prints to check critical colors
Impact of Paper Stock on Color Reproduction
Your choice of printing material makes a big difference in how colors look. Smooth-coated paper reflects light differently than rough uncoated stock, which changes how vibrant colors appear. Matte surfaces scatter light because of tiny bumps, so colors won't look as rich as they do on glossy paper.
Paper's brightness, texture, and finish all affect how it absorbs color. To name just one example, see how matte stock spreads halftone dots wider and absorbs more light. A 50% halftone might look more like 75% coverage on these surfaces.
Printing on kraft or colored materials brings its own challenges. Browns, greens, and oranges look quite different than they do on white paper. Print shops adjust their machines for each material type to keep colors consistent.
Getting the same results every time needs proper color adjustment and profiling. This gives print shops a way to match colors exactly on each run, no matter what material they use. The core team also thinks about finishing options like lamination or varnish since these can change how colors look in the final product.
Essential File Setup Steps
Quality file preparation is the life-blood of successful sticker printing. The right settings in your design software will help you avoid common printing mistakes and give you the best results.
Setting Document Color Mode to CMYK
Your design should start in CMYK mode to prevent unexpected color changes that happen during RGB conversion. Adobe Photoshop users can find this setting through Image > Mode > CMYK Color. Adobe Illustrator users should go to File > Document Color Mode > CMYK Color.
Here's how to get consistent results on different design platforms:
- Adobe InDesign: Go to Window > Swatches and Window > Color
- Corel Draw: Pick Fill tool and click Fill Color Dialog
- Microsoft Publisher: Select Tools > Commercial Printing Tools > Color Printing
Configuring Resolution and Bleed Settings
Quality sticker printing needs exact resolution settings. Your files should maintain 300 PPI (pixels per inch) to get sharp, professional results. You can find your artwork's PPI by dividing its width by your desired print size.
Bleed settings are crucial for edge-to-edge printing. Here are the standard requirements:
- 0.1 inches for most sticker products
- Extra 0.25 inches from trim lines for critical elements
- Safe zone should be at least 0.5 inches from document edges
Converting RGB Images to CMYK
RGB colors look vibrant on screen but often print differently. Professional-grade CMYK profiles will translate colors accurately. Here's what you should do:
Keep your original RGB file as backup before any color adjustments. Use your design software's built-in tools for conversion. Check your converted colors in CMYK preview mode to make sure they look right.
These color issues come up often:
- Blurry black text from four-color mixing
- Bright RGB colors becoming duller
- Colors looking different across materials
Simple black (K100) works better than rich black mixes for small text. Printed results usually look darker than what you see on screen. A soft proof before finalizing your design will ensure accurate colors.
Printers might not accept files with wrong color modes and ask for changes. Good file setup saves time and leads to better print quality. RGB to CMYK conversion lets you control the final look better.
Color Profile Management
The right color profiles play a vital role in getting precise color reproduction for sticker printing. Print shops will recommend specific CMYK profiles that match their press requirements and methods.
Choosing the Right CMYK Profile
GRACoL is the revolutionary force for sheetfed reproduction, which makes it perfect for custom sticker work. SWOP 3 or SWOP 5 profiles work better for web press printing. European markets rely on FOGRA CMYK profiles as their region-specific color standards.
Here's what you need to think over when picking a profile:
- Your printer's press-specific profiles
- Paper stock properties
- Regional printing standards
- Your finishing method choices
The right profile keeps colors looking consistent through the transformation process. Converting between color models needs mapping to a smaller gamut space. Understanding these profile differences helps keep your design looking great from screen to final print.
Color Calibration Techniques
Your monitor settings are the starting point for accurate color calibration. Room lighting changes how colors look on screen. You'll get better results in darker rooms. Here's the quickest way to calibrate:
- Make duplicate files for RGB reference
- Put reference and target files next to each other
- Turn on soft proofing with destination space
- Check Black Point Compensation settings
- Look at different rendering intents to find the best conversion
Print shops employ white underprint techniques on clear and colored materials. They put down a white base layer under CMYK colors, which gives vibrant results on non-white surfaces. This step is crucial for kraft, gold, and silver substrates.
Color matching problems often come from:
- Different screen brightness levels
- Various paper stocks
- How ink gets absorbed
- Effects from finishing
Color calibration tools help line up what you see on screen with your printed results. On top of that, it's worth ordering sample prints for projects where color matching is critical.
Your files should keep their embedded CMYK profiles to get consistent results across multiple print runs. These profiles give printers a solid starting point, even when they need to adjust things like total ink limits for different papers.
Soft proofing tools let you preview before printing. When gamut warnings show problem areas, create HSL adjustment layers and call it "CMYK conversion". Start by adjusting saturation for affected colors, then work on hue if needed.
Note that getting colors 100% accurate just isn't possible. But good profile management and calibration techniques will get you the best color quality. Hard copy proofs ended up being the most reliable way to check color accuracy for your sticker projects.
Quality Control Measures
Quality control in sticker printing requires careful attention to detail during production. Professional printers use well-laid-out methods to keep consistency in large orders.
Using Soft Proofing Tools
Soft proofing lets you preview final print outcomes on adjusted monitors. This method saves time and materials by spotting potential issues before physical printing starts. Here's what you need to do for accurate soft proofing:
- Set up your monitor in controlled lighting conditions
- Install the right ICC profiles for your printing device
- Use Black Point Compensation to preserve shadow details
Professional software's soft proofing tools come with distinct advantages. Photoshop works with both RGB and CMYK profiles, while Lightroom only handles RGB profiles. These tools help designers simulate paper color and ink effects to match colors precisely.
Common Color Issues and Solutions
Color-related challenges pop up often in sticker printing. Purple blues appear when cyan and magenta values are too close together. You can fix this by keeping at least a 30-point difference between these values.
Other common problems include:
- Neutral grays that drift to unwanted tones
- Black text that looks fuzzy or blurred
- Pictures that print differently than they show on screen
Rich black formula (C:60, M:40, Y:40, K:100) creates deep blacks without muddiness. For sharp black text, you should use 100% black (K) channel only.
Print Test Guidelines
Print tests are vital before starting large production runs. Professional printers suggest you:
- Create certified proofs with Ugra/FOGRA Media Wedge scale measurements
- Compare initial prints with approved proofs
- Keep records of printer settings and color matching
- Check results under standardized lighting
Temperature and humidity levels affect how ink sticks and dries. Therefore, steady environmental conditions during production will give reliable results.
Quality control works best when printers check three vital stages:
Prepress checks confirm file preparation and proofing accuracy. In-process monitoring keeps colors consistent and registration precise. Post-printing inspection makes sure finished products meet quality standards.
Professional printers document every change and decision during production. This practice helps improve processes and maintains consistency in future print runs. These quality control steps will give sticker prints that match design expectations and reduce expensive reprints or unhappy customers.
Material-Specific Considerations
Each printing material just needs specific color adjustments to get the best results in sticker production. Material-specific needs will give a precise color reproduction on substrates of all types.
Vinyl Sticker Color Requirements
Vinyl stickers come with their own set of color management challenges. Light-colored surfaces need exact ink combinations to stay vibrant. Professional printers use white underprint techniques beneath CMYK colors to get consistent results on non-white surfaces.
Your vinyl's color reproduction depends on several things:
- Base material's color changes the final look
- Surface texture affects how ink gets absorbed
- Weather conditions change color stability
- Finishing methods change how colors look
Color calibration becomes vital for vinyl as some shades look different based on the substrate's features. Pantone color matching works best, especially when you have designs with large solid color areas.
Paper Sticker Color Adjustments
Paper stickers need special attention based on their surface properties. Matte paper is affordable but has issues with lighter colors. These surfaces soak up more ink, which can make colors look less vibrant.
Surface features substantially affect color results:
- Glossy paper creates sharper prints and absorbs less ink
- Satin finishes give balanced color definition with some shine
- Matte surfaces spread halftone dots wider and change color density
Kraft and specialty papers make things more complex. Light colors, especially yellows, barely show up on clear stickers placed on dark surfaces. White ink needs special spot color printing methods on materials like holographic or silver substrates.
Getting the best results on paper stocks takes a few steps:
Paper's brightness level directly affects how vibrant colors look. Texture differences between coated and uncoated stocks change light reflection patterns. You'll need to adjust color values based on the paper's specific features to keep your design looking right.
Color management becomes crucial when printing on specialty materials. Browns, greens, and oranges look quite different compared to standard white surfaces. Professional printers tackle these issues through specific calibration processes for each material.
Waterproofing choices affect your color options too. Pigment ink with matte paper resists water well but needs special printing equipment. Clear coating and lamination protect better but might change how colors look in the end.
The right material choice and color adjustments help printers keep things consistent across different substrates. This approach ensures your final sticker product matches the original design whatever material you pick, while meeting all your specific needs.
Conclusion
The right CMYK file preparation is vital to achieve professional sticker printing results. Designers can ensure their stickers match intended designs when they select the right color mode, set up files correctly and manage profiles properly.
Quality control drives the entire printing process. Soft proofing tools detect issues early, and print tests verify color accuracy before large production runs begin. The choice of material substantially affects final outcomes. This makes substrate-specific color adjustments necessary for the best results.
Professional printers recommend these key practices:
- Setting up files directly in CMYK mode
- Maintaining 300 PPI resolution with appropriate bleed
- Using material-specific color profiles
- Running print tests before large orders
- Documenting color decisions for consistency
Want to see these guidelines in action? Start your custom sticker order with us today and discover the difference professional CMYK preparation makes in your final prints.
Note that successful sticker printing combines technical expertise with hands-on experience. Color matching can be challenging, but these proven processes ensure consistent, high-quality results in all your sticker projects.
FAQs
Q1. How do I prepare my artwork for sticker printing in CMYK format? Start by setting your design software to CMYK color mode. Ensure your file resolution is 300 PPI and include a 0.125-inch bleed. Convert any RGB images to CMYK, and use appropriate color profiles for your printer and material. Soft proof your design to check for color accuracy before finalizing.
Q2. What's the best file format for CMYK sticker printing? For professional sticker printing, PDF is widely accepted and versatile. TIFF is also excellent for preserving image quality, especially for photos. For vector graphics like logos, EPS is ideal. Avoid using JPG or PNG for professional print jobs, as they may compromise quality or aren't suitable for CMYK printing.
Q3. Why is converting to CMYK important before printing stickers? Converting to CMYK before printing is crucial because it aligns your design with the four-color printing process (Cyan, Magenta, Yellow, Black) used by printers. This conversion ensures that the colors in your final printed stickers will match your design intent as closely as possible, avoiding unexpected color shifts.
Q4. How does the choice of material affect sticker color reproduction? Different materials can significantly impact color reproduction. Vinyl stickers may require white underprinting for vibrant colors, especially on non-white surfaces. Paper stickers vary based on finish - glossy papers yield sharper prints, while matte surfaces may absorb more ink, affecting color density. Always consider the material's properties when adjusting your design colors.
Q5. What quality control measures should I take when printing CMYK stickers? Implement soft proofing to preview print outcomes on your monitor. Run print tests before large production runs to check color accuracy. Use certified proofs with color measurement scales. Review prints under standardized lighting conditions. Maintain consistent environmental conditions during printing, and document all color decisions for future reference.